Prevention and mitigation of damage problems
Ua Scientific and Technical Center provide integrated approach to prevention and mitigation of various damage problems in production such as
The following effective technologies are employed for prevention and mitigation of damage problems:
- Efficient technique to prevent scale and corrosion (the so-called Squeeze) implies squeezing a combination of chemical agents into the near wellbore formation zone followed by its gradual backflow (withdrawal) during stimulation. The technology ensures 3-8 times longer time between failures for ESPs
- Deployment of submersible downhole containers – dispensers for inhibiting scale, heavy oil deposits and corrosion
- Placement of dosing containers filled with inhibiting compositions below the downhole motor of the ESP ensuring the following results:
- Prevention of scaling, heavy oil deposits and corrosion within the area of the downhole motor, movable working parts of the ESP and tubing
- Increased time between failures for ESPs – double the original life span and longer
- Reduced operating costs for inhibiting compared to other prevention and mitigation
Corrosion
Corrosion is the destruction of metal or alteration of its properties due to its exposure to external environment. In a narrower sense corrosion is understood as metal failure caused by environmental exposure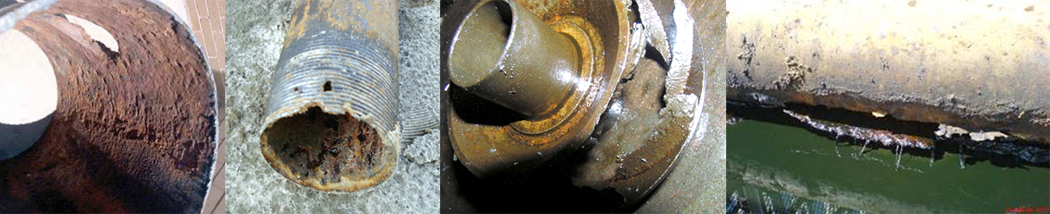
Based on the mechanism the following types of corrosion are identified:
- Electrochemical (carbon dioxide, hydrogen sulfide, oxygen, acid)
- Microbial / biological (sulfate reducing bacteria, hydrocarbon oxidizing bacteria, thionic bacteria, iron-depositing bacteria and the like)
- Erosive
Based on its form the following types of corrosion are identified:
- Massive (uniform attack)
- Non-uniform
- Pitting (localized/selective)
- Rill (channel/groove)
- Mesa corrosion
Heavy oil sediments
Heavy oil deposits (asphaltenes, resins and paraffins) are dark brown or black solid to thick salvy substance with high viscosity which becomes slightly less viscous at elevated temperaturesThe chemical composition of the heavy oil deposits may vary in a very wide range depending on the genetic origin, age, properties and composition of the produced oil and some other factors including reservoir geology, production technology, pressure and temperature regimes and fluid dynamics; properties of reservoir fluids, reservoir development and production conditions
Heavy oil deposits contain paraffins, resins, asphaltenes, oils, sulfur, metals and minerals as salt solutions of organic acids, complex compounds or colloid-dispersed inorganic substances. Heavy oil deposits also contain some water with dissolved salts, these are predominantly chlorides and sodium, calcium and magnesium hydrogen carbonates as well as sulphates and carbonates. The deposits also contain entrained solids in the form of clay particles, quartz sand grains, iron scale (cinder) and similar