Well stimulation (Water conformance control)
When developing an oil or gas field the Operator frequently faces the problem of unwanted water production due to formation and injected water breaking through high-permeability reservoirs and layers to producing wells thus decreasing oil recovery rates and causing decline in overall oil production. The well production potential is not realized in this case
The solution to this problem in terms of fluid dynamics and as a result higher oil recovery rates comes down to controlling fluid flow in-situ (i.e. oil, formation water, emulsions with dissolved gases)
The solution to this problem in terms of fluid dynamics and as a result higher oil recovery rates comes down to controlling fluid flow in-situ (i.e. oil, formation water, emulsions with dissolved gases)
Ufa Scientific and Technical Center development a line of chemical products including phase-selective and permeability-selective agents to use for flow diverting in unswept areas with by-passed oil
The main idea of the technology is to create gel screens or flow barriers in channels with low resistance to fluid flow flushed by injected water. In the course of treatment a gellant is pumped into an injector which contains unlinked polymer system with the initial viscosity comparable to water viscosity. Under reservoir conditions the gallant turns into a cross-linked polymer system with significantly higher viscosity. Such screens increase fluid flow resistance (reduce permeability) in water saturated parts of the reservoir, change and divert flow paths and prevents swelling of reservoir rock
The workflow pattern for field operations is described below:
- Screening and selection of test areas with candidate wells based on highest reserve potential
- Efficiency analysis and review of results from previous conformance / water control operations performed on the same field
- Feasibility studies for treatment techniques; prediction of post-treatment technological effects
NGT-CHEM CONFORMANCE / WATER CONTROL TECHNOLOGY
The treatment technique for oil reservoirs using NGT-Chem composition is based on a water-isolation screen set in flushed reservoir layers and drainage zones with highest permeability to increase sweep efficiency
- High-viscosity composition containing NGT-Chem-2 with structure-forming fillers (microcalcite and lignosulfonate) is pumped into the reservoir to reduce the permeability of fractures and super reservoirs
- Then the main volume of the composition is pumped which consists of a water-based solution of NGT-Chem-6 with microcalcite. The slugs are pumped in a sequence separated by fresh water cushions V=9 m3 prior and following each slug
- The injected composition invades water saturated layers without clogging oil saturated parts of the reservoir. In the results of treatment gel forms under reservoir conditions which shuts off flushed channels with low fluid flow resistance (fractures and super reservoirs) and redistributes fluid flow paths with isolated flushed intervals
- Rheological properties of the formed gel correspond to the thixotropic pseudoplastic body of the coagulation structure which prevents fluid filtration in the water saturated part of the reservoir, redistributes fluid flow paths and improves conformance of the flood front
- NGT-Chem-6 also acts as a mild base capable of neutralizing weak acids contained in oil. In the result of such reactions the contact angle of the reservoir rock (interface angle) changes increasing phase permeability relative to oil and also increasing oil mobility with slight oil emulsification. All these effects combined result in lower watercut and higher oil rates in treated wells within the reaction area
- The injected composition penetrates water bearing layers bypassing oil saturated parts of the reservoir. High conductivity flow paths become isolated. The squeezing by fresh water cushions helps to place the gellant before the flood front in low permeability zones of the reservoir
- The injection is followed by sufficient volumes of water so that the last slug of the sediment and gel-forming composition in the most permeable zone is placed ahead of the slug front in the least permeable zone
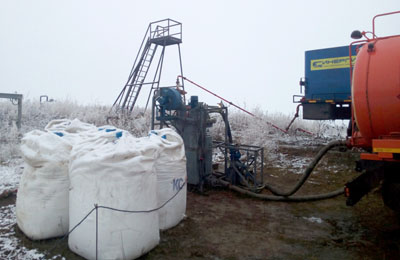
- After squeezing with bottom water the well is shut for 48 hours for completion of the gel formation reaction. After shut-in period is over the water injection slowly resumes with gradual increase in injection volumes to achieve pre-treatment rates
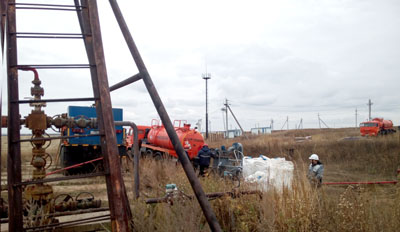
OPERATIONAL BENEFITS OF NGT-CHEM TECHNOLOGY APPLICATION
The operation benefit of NGT-Chem application is the incremental oil production from the reservoirRedistribution of flow paths, alteration of surface-active properties of the reservoir rock and formation fluids result in higher sweep efficiency, changes in the contact angle of the reservoir rock (interface angle) and oil emulsification thus reducing watercut and increasing oil production rates. The benchmark analysis to evaluate efficiency and results relies on historic production from the selected area
APPLICATION CRITERIA FOR NGT-CHEM INTEGRATED TECHNOLOGY
- NGT-Chem integrated technology is recommended for oil fields with both sandstone (siliciclastic) and carbonate reservoirs characterized by insufficient and non-uniform waterflood displacement efficiency due to high vertical and lateral permeability heterogeneity (anisotropy Kv/Kh)
- The best candidates for NGT-Chem injection are wells which tapped the entire section of the producing reservoir with well-defined lithological heterogeneity and permeability anisotropy and reservoir units continuously traced from injection wells to nearby producing wells without any faulting. The technology is best designed for injection wells in pressure communication (connectivity) with wells producing liquid with high water cut from flooded reservoir zones
- Wells for NGT-Chem injection are selected on the basis of G&G and production data analysis for specified study zones which allows identifying the extent of the injection zone, correlating it to producing wells with water breakthrough and establishing pressure communication between the injection and production wells